StarLine Manufacturing
Take a look at StarLine's full-cycle production process.
StarLine places a large emplasis on 2 key concepts when it comes to production: automation and quality control.
World-class research, developement, and manufacturing facilities at the StarLine headquarters - the largest and most advanced hi-tech production plant of its kind in Europe, employing the strictest quality control procedures to ensure unparalleled quality, super-realiable performance, and hassle-free day-to-day operation for the end-user.

Automation
StarLine production is over 90% automated, excluding any human error, and making operations faster, safer, and more efficient.

Quality Control
StarLine employs the strictest quality control procedures - both automated and manual - at every stage of the manufacturing process.
Production Facilities and Equipment
The company’s production facilities are located in St. Petersburg, Russia, as well as in the automotive industrial area in the Leningrad Oblast, covering the area of over 70 000 sq. m.
StarLine manufacturing is focused on high-quality mass production, automated at all stages, using the Industry 4.0 standards.
Automotive security equipment under the brand of StarLine is created using world’s most reliable top-of-the-line machinery, such as:
Panasonic SP-70 screen printer (Japan); high-performance Panasonic NPM-W pick and place modular system (Japan); Senju SNR-1065 convection oven (Japan); 3D Koh Young solder paste inspection (Korea); Koh Young Zenith 3D automated optical inspection (Korea); Takaya APT-1400F high-speed in-circuit monitoring system (Japan)… to name a few.
StarLine focuses equally on – and allocates equal resources toward – research, developement, and production. The company is on the path of continuous evolvement and improvement in all three areas.
All the existing manufacuring and production equipment at StarLine is constantly monitored and undergoes testing, professional calibration, and routine maintenance at regular intervals, ensuring that chances of factory defects in our products are minimal*
* Compared to other manufacturers of similar products, whose factory defect rate is up to 40%, StarLine’s factory defect rate is less than 5%.
The company continuously invests in new equipment and seeks to improve its practices and streamline production. At the moment, the company has the following facilities on site (most, if not all, other automotive security equipment manufacturers use third party contractors for these services; we do it on-site):
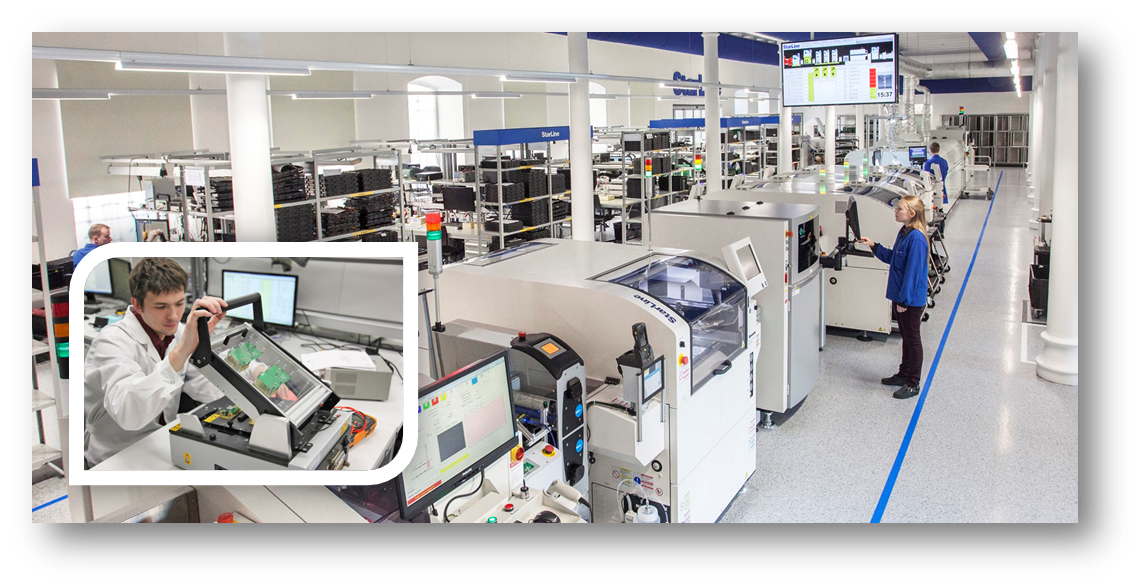
Production of Electronics (PCB)
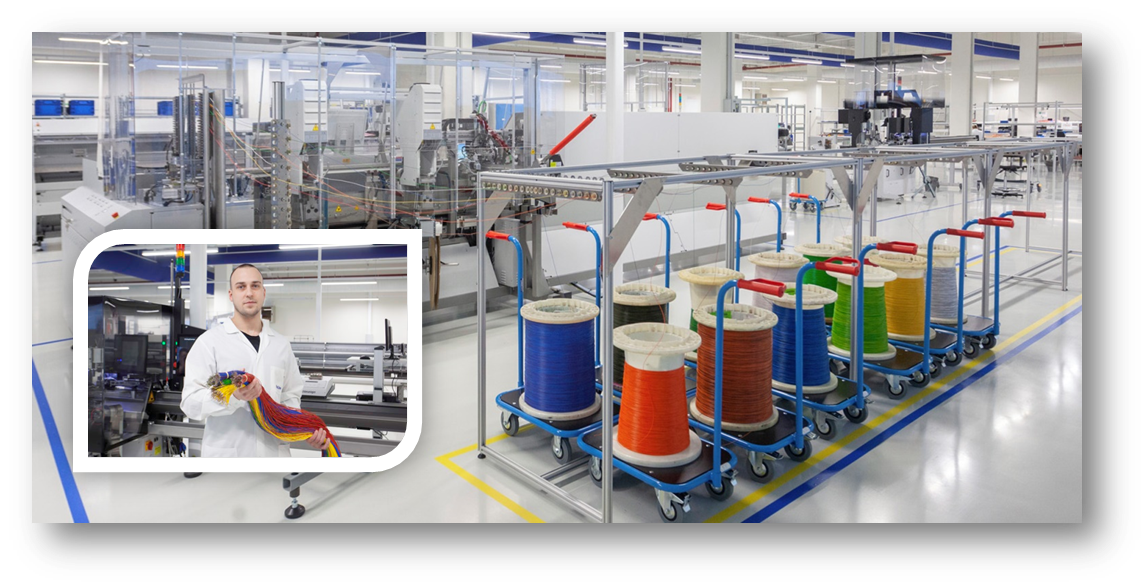
Cable Assembly
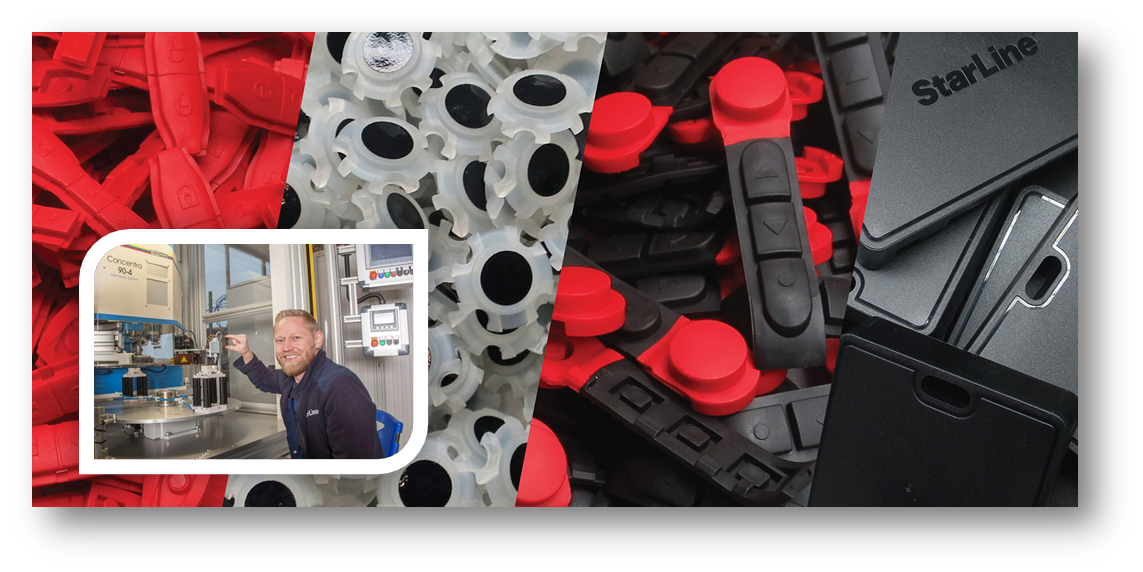
Plastic Injection Moulding
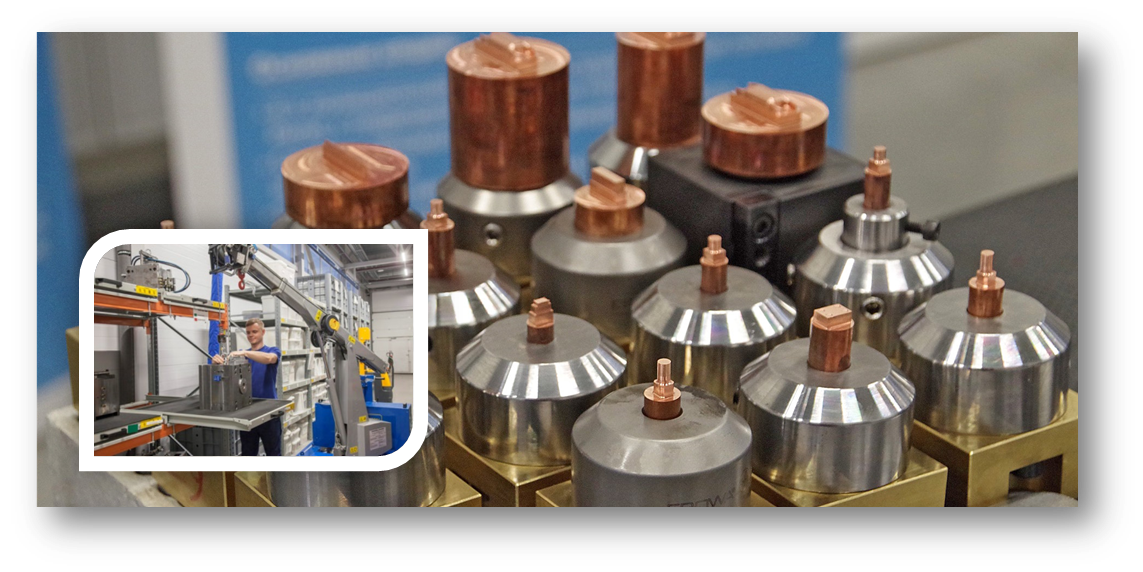
Press Form Modelling & Production
Collective Quality Management & Control

Digital automated production control system.
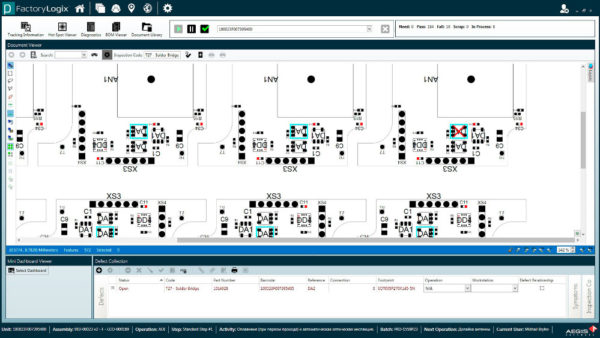
The key advantage of the StarLine production is its collectiveness. From prototype development and thorough testing to serial production and assembly of a finished product – all stages of production are migrated, and it’s all done on-site. Our production team consists of over 1000 members with various skills and competences, allowing us to carry out the production process from A to Z, without having to commission any third parties at any point of the production process.
Efficiency of operation is further streamlined through automation and robotisation of most stages of the manufacturing process. The automation of the manufacturing process at StarLine exceeds 90%, in accordance with the “Industry 4.0” standards . StarLine uses the latest industry specific equipment, as well as the most advanced digital software for automated production management and quality control, including SAP, FactoryLogix, Team Center, and others.
StarLine produce holds international certification – E1 (TUV SUD, Germany) and complies with the ISO 9001: 2015, GOST R ISO 9001: 2015 quality management standards.
The Manufacturing Process
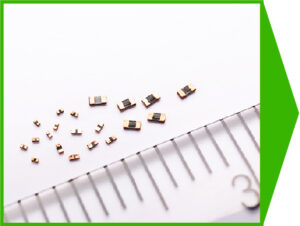
Step (1) One
Input quality control of the components.
Registraqtion of components.
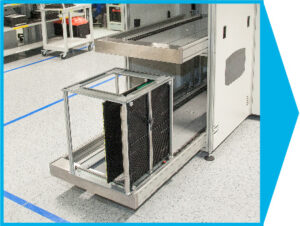
Step (2) Two
Automated PCB loading.
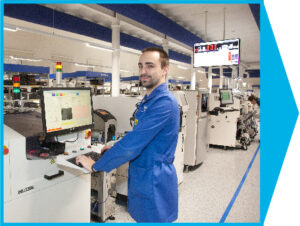
Step (3) Three
PCB marking.
Registraqtion of components.
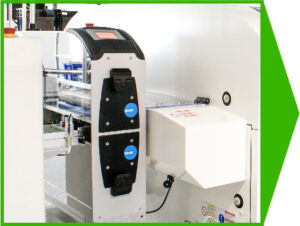
Step (4) Four
Teknek PCB cleaning.
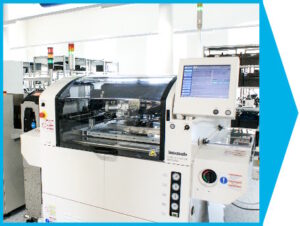
Step (5) Five
Solder paste application.
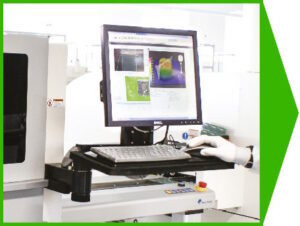
Step (6) Six
100% 3D quality control of solder paste application.
Date and time of the control procedure + defects / faults (if any) documented.
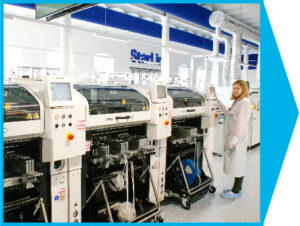
Step (7) Seven
Placement of surface mounted components.
Date and time of mounting,
location of components on the PCB, component binding to the PCB.
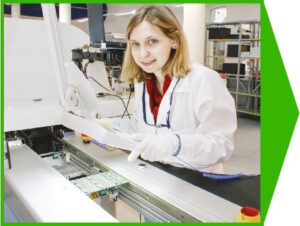
Step (8) Eight
Inspection of the first PCB with components.
Date and time of inspection and inspector’s ID + defects / faults (if any) documented.
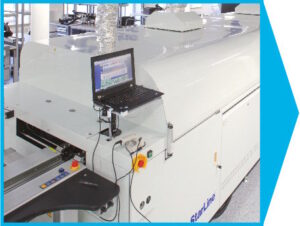
Step (9) Nine
Soldering and reflow.
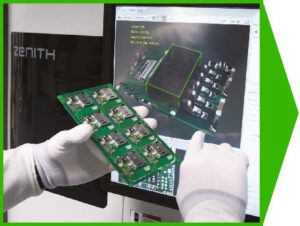
Step (10) Ten
100% 3D quality control of the soldered PCB.
Date and time of control + defects / faults (if any) documented.
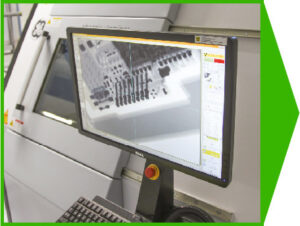
Step (11) Eleven
X-ray control.
Date and time of control + defects / faults (if any) documented.
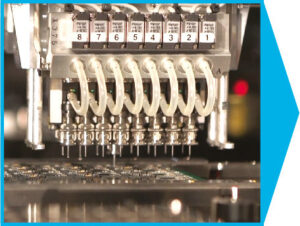
Step (12) Twelve
Placement of throughly mounted components.
Date and time of mounting,
location of components on the PCB, component binding to the PCB.
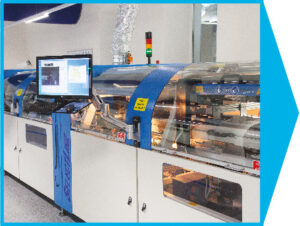
Step (13) Thirteen
Selective soldering of throughly mounted components.
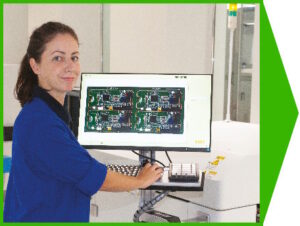
Step (14) Fourteen
100% quality control of the soldered PCB.
Date and time of control + defects / faults (if any) documented.
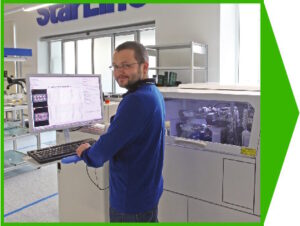
Step (15) Fifteen
In-circuit testing.
Date and time of control + defects / faults (if any) documented.
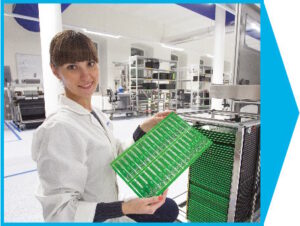
Step (16) Sixteen
Automated PCB unloading.
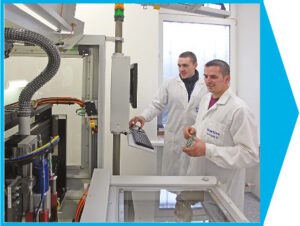
Step (17) Seventeen
Automated PCB separating.
Date and time of the operation entered in the logs.
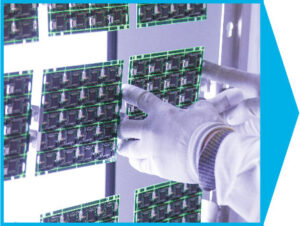
Step (18) Eighteen
PCB washing.
Date and time of the operation entered in the logs.
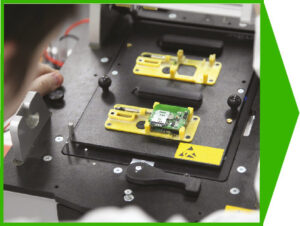
Step (19) Fifteen
Complete functionality testing.
Date and time of testing + defects / faults (if any) documented.
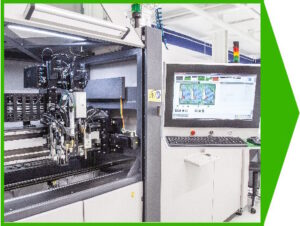
Step (20) Twenty
Selective waterproofing.
Date and time of testing + defects / faults (if any) documented.
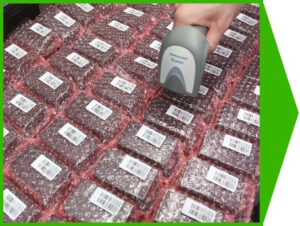
Step (21) Twenty One
Final output PCB control.
Date and time of inspection and inspector’s ID + defects / faults (if any) documented.
From A to Z
From theories, ideas, and research — to prototype developement — to full-cycle production and testing of the finished product — to the implementation of the concepts and solutions by suitably qualified professionals — the end-user can be sure that they are getting both – products and services – that the manufacturer is in full control of!
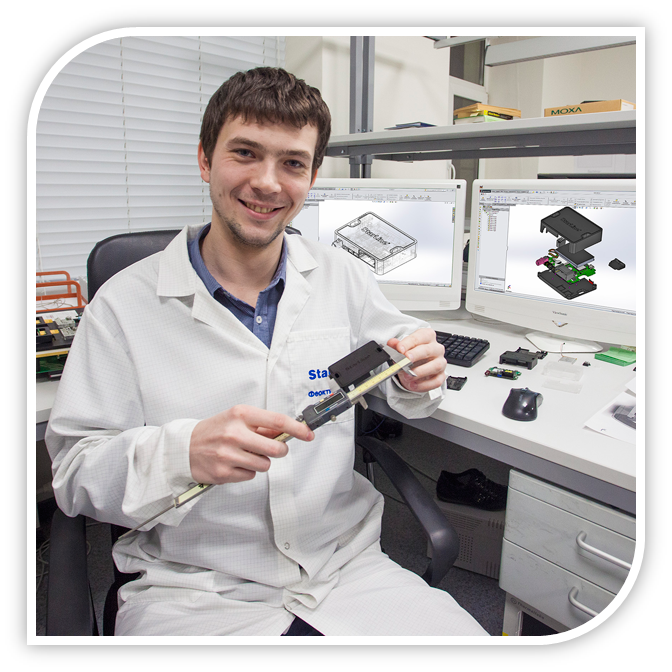
Research, Prototype Developement, Testing, Production, Quality Control, Storage - All Done On-Site!
✅ Intangible concept and ideas;
✅ Research and developement; surveying;
✅ Prototype creation;
✅ Prototype testing;
✅ Developement of software;
✅ Developement and manufacturing of hardware;
✅ Developement and manufacturing of peripherals;
✅ Assembly;
✅ Testing of the finished product;
✅ Streamlining of the finished product;
✅ Proper storage;
✅ Packaging and presentation.
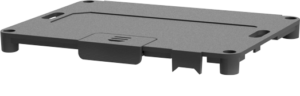
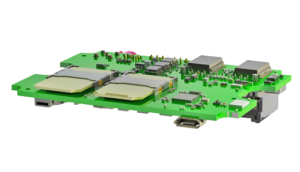
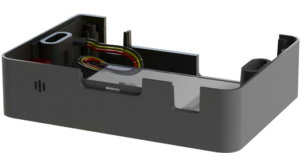
Testing and Storage
StarLine’s automotive security equipment goes through various climatic, electrostatic, and endurance tests, as well as cryptographic tests, immunity to conductive / radio / radiation interference, and numerous other tests in accordance with GMW.
As described above, StarLine production is based on an integral approach, where every part of the process – from prototype development to storage and shipping – is strictly monitored and controlled by on-site personnel.
The manufactured equipment undergoes advanced multi-stage testing prior to storage. Particular attention is paid to storage conditions of electronic components that meet international standards.
StarLine conducts the following types of tests of its electronic produce:
✅ Climatic / environmental testing;
✅ Electrostatic testing;
✅ Electromagnetic interference resistance testing;
✅ Radiowave interference resistance testing;
✅ Spurious emission (radiation) interference testing.
Plastic components undergo the following tests:
✅ Heat resistance;
✅ Fire / inflammation resistance;
✅ Bending, tensile, compressive strength;
✅ Impact strength;
✅ Abrasion resistance;
✅ Colorimetric properties (color, light transmission, etc.).
Quality You Can Trust
... as do millions of others across the world!
Due to state-of-the-art production facilities, complex testing and monitoring procedures, rigid quality control protocols, and modern storage facilities, the equipment produced at the StarLine manufacturing plant is extremely durable in design and stable in performance.
Since 1988, year after year, the company has proven its stance on quality and dedication to continuous technological advancement. As a result, today, millions of corporate and individual consumers worldwide trust us, and our innovative manufacturing practices and award-winning concepts and solutions in the automotive industry are recognised across the world by numerous reputable and established accreditation and certification bodies.
Moreover, StarLine is one of the very few aftermarket automotive security equipment manufacturers in the world, whose produce has received homologation and is used as a genuine accessory of factory vehicles, by a number of vehicle manufacturers, such as Ford, Toyota-Lexus, the VAG group… and over 30 others.
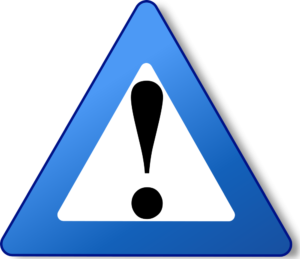
StarLine employs the strictest quality control procedures, ensuring that only the produce that has successfully completed and passed all the aforementioned testing procedures leaves the production premises and make it to the end-user.
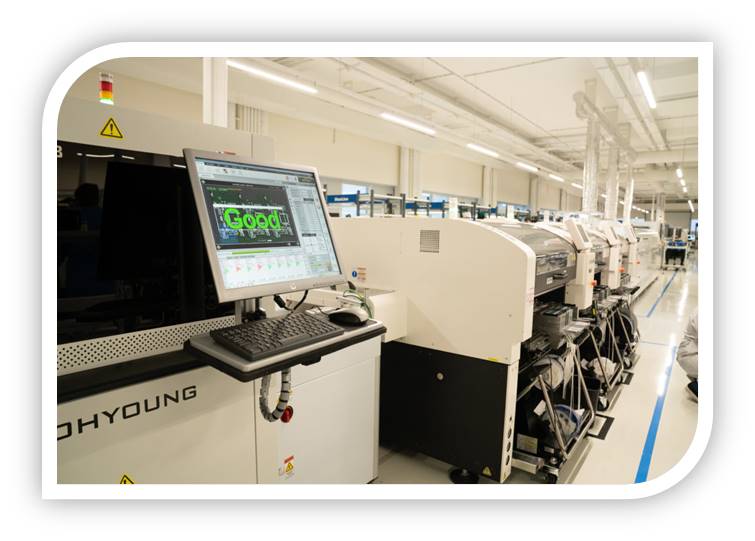
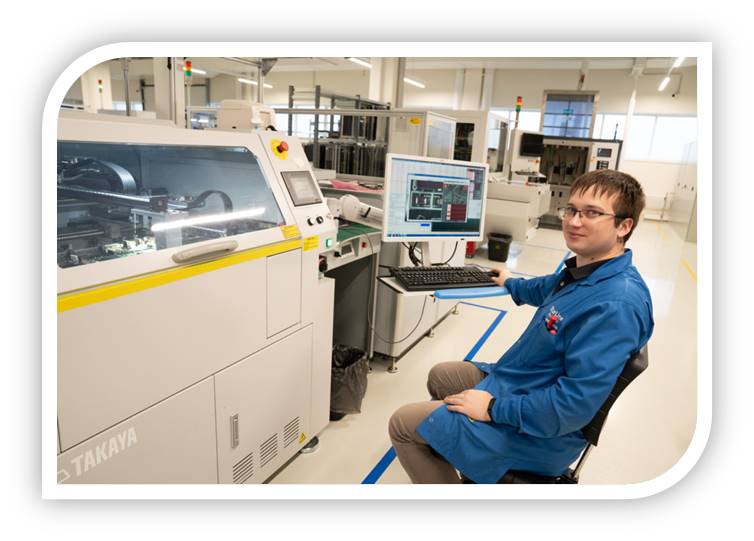
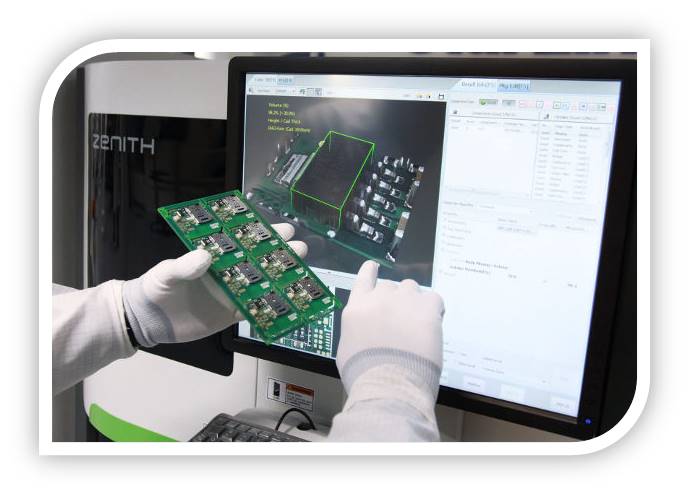
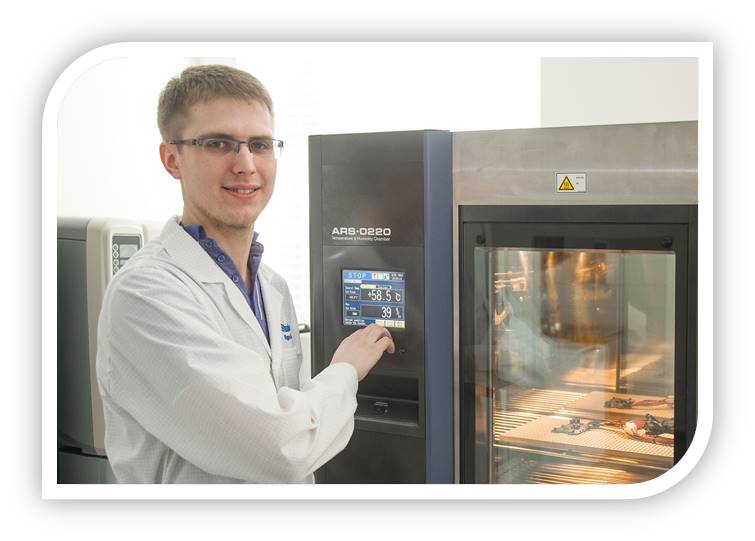
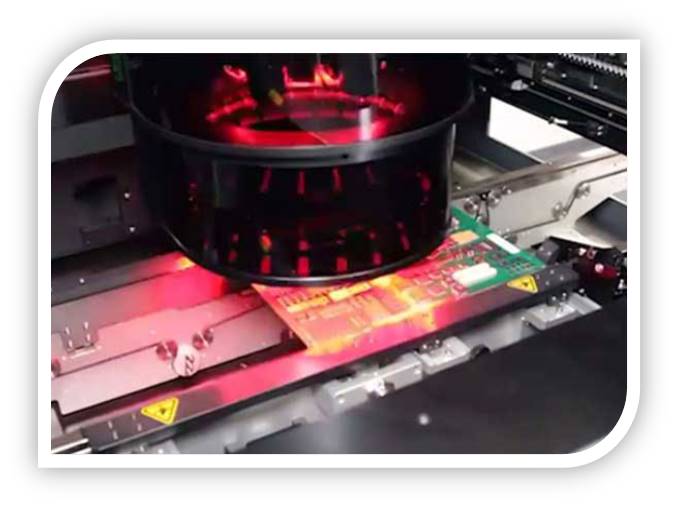
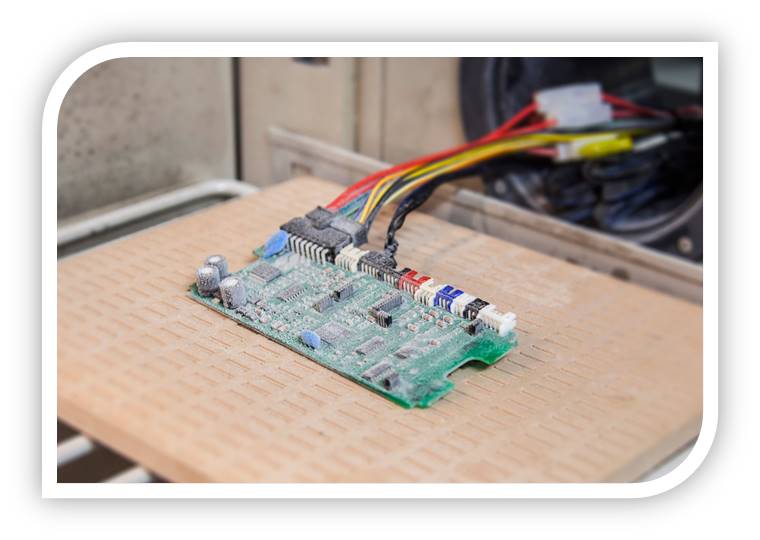
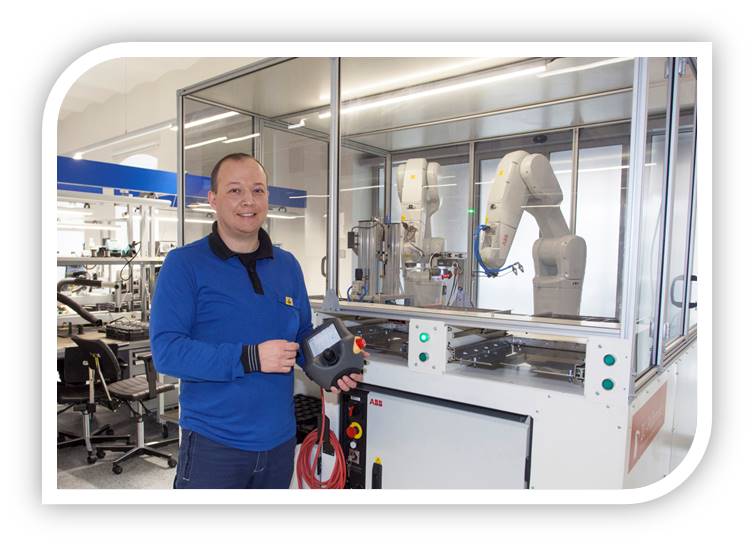
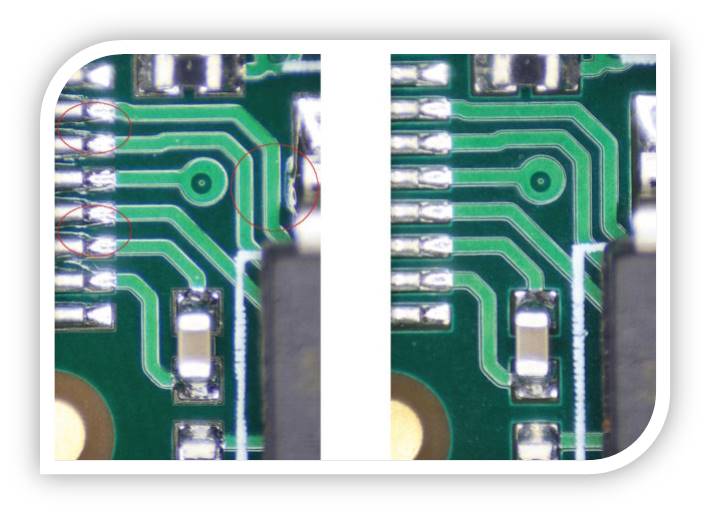
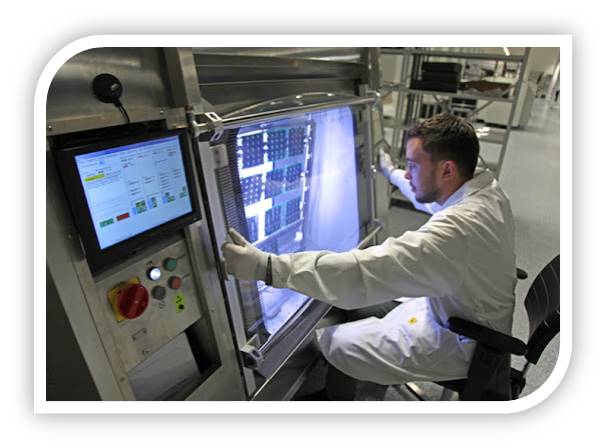
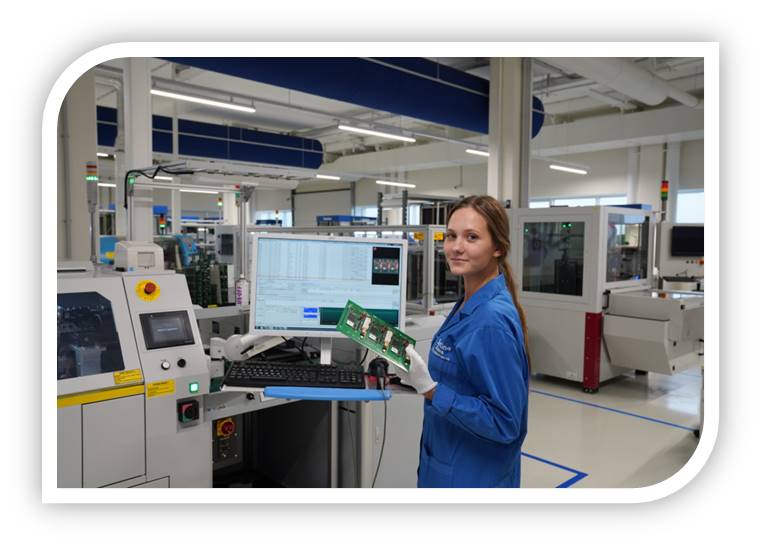
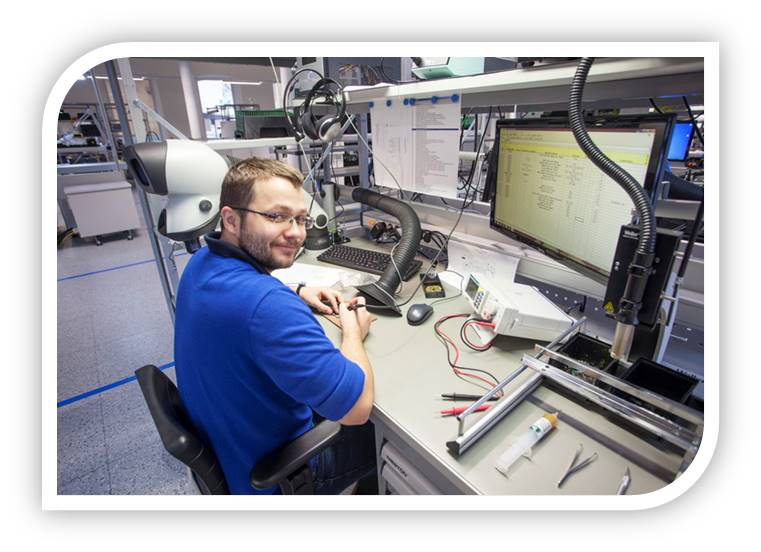
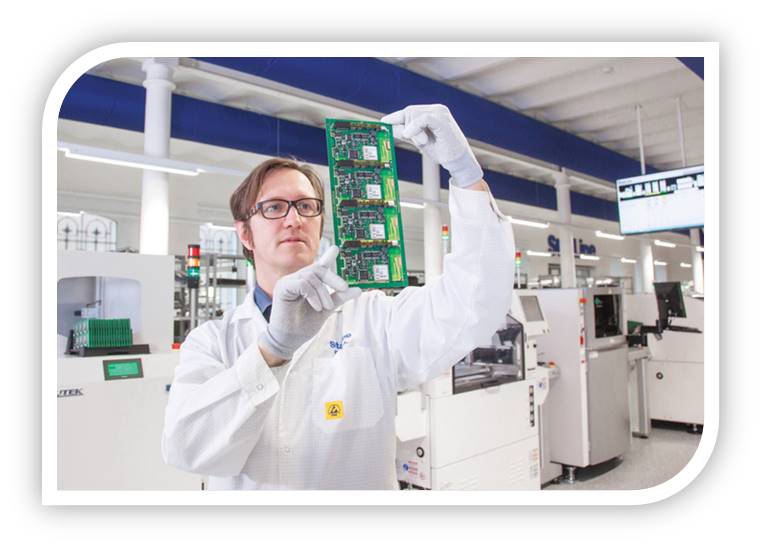
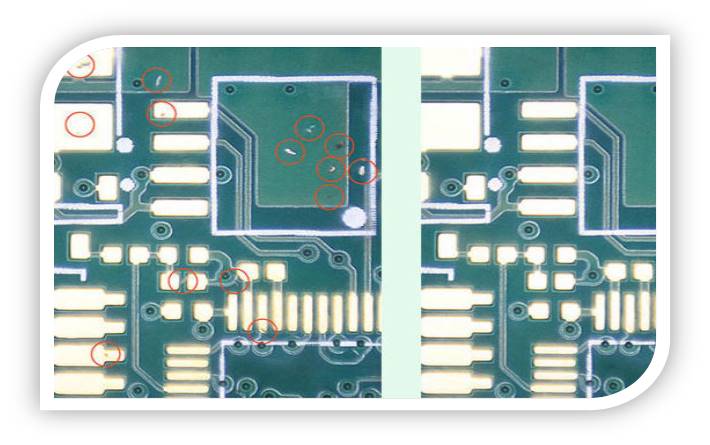
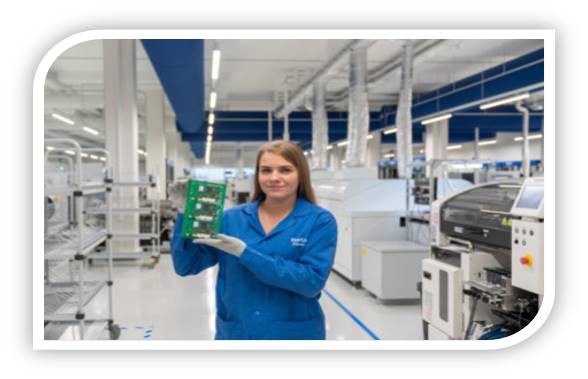